Applications of Injection Molding
how injection molding impacts industries, reduces costs, and ensures precision. Learn about materials, processes, and benefits here.
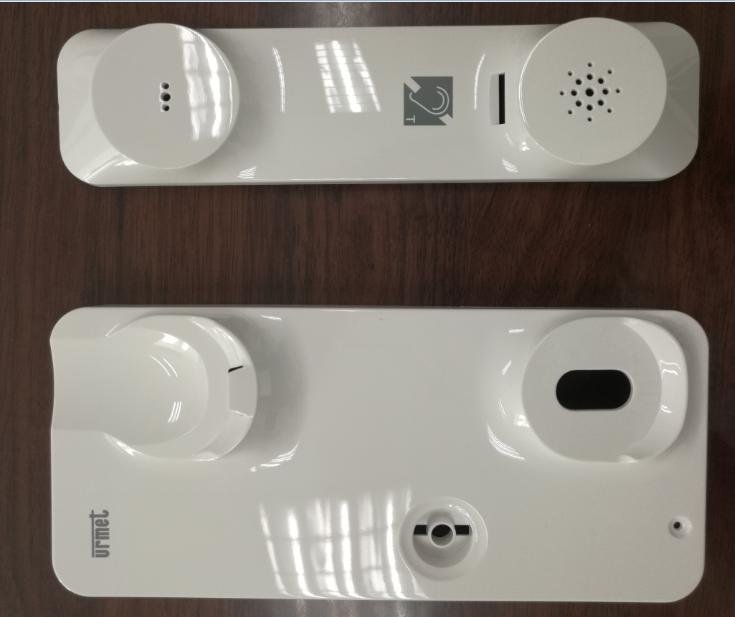
How Injection Molding Shapes Modern Manufacturing
Injection molding is one of the most important manufacturing processes in the modern world. It’s used to create everything from car parts to medical devices, consumer goods, and even toys. The process is efficient, cost-effective, and versatile, making it a cornerstone of industries worldwide. In this article, we’ll explore how injection molding works, its benefits, and why it’s so widely used.
Table of Contents
Heading | Description |
---|---|
What Is Injection Molding? | A simple explanation of the injection molding process. |
Benefits of Injection Molding | Why it’s a preferred method for manufacturing. |
Materials Used in Injection Molding | Common plastics and their applications. |
The Injection Molding Process | Step-by-step guide to how it works. |
Applications of Injection Molding | Industries and products that rely on this process. |
Cost-Effectiveness of Injection Molding | How it saves money in production. |
Challenges in Injection Molding | Common issues and how to overcome them. |
Sustainability in Injection Molding | Eco-friendly practices in the industry. |
Choosing the Right Injection Molding Partner | How to find a reliable supplier. |
Future Trends in Injection Molding | Innovations shaping the industry. |
What Is Injection Molding?
Injection molding is a manufacturing process that produces parts by injecting molten material into a mold. The material, usually plastic, is heated until it becomes liquid, then forced into a mold cavity where it cools and hardens into the desired shape.
This process is ideal for creating large quantities of identical parts with high precision. Whether it’s a simple bottle cap or a complex automotive component, injection molding can handle it all.
Benefits of Injection Molding
Injection molding offers several advantages that make it a go-to method for manufacturers:
- High Precision: The process ensures consistent and accurate production.
- Scalability: It’s perfect for mass production.
- Material Variety: A wide range of plastics can be used.
- Cost Efficiency: Once the molds are made, the cost per part is low.
- Durability: The final products are strong and long-lasting.
These benefits explain why injection molding is used in industries like automotive, electronics, and healthcare.
Materials Used in Injection Molding
The choice of material is crucial in injection molding. Here are some commonly used plastics:
- ABS (Acrylonitrile Butadiene Styrene): Known for its strength and impact resistance.
- Polycarbonate: Transparent and highly durable, often used for lenses and medical devices.
- Polypropylene: Lightweight and flexible, ideal for packaging and containers.
- Nylon: Strong and resistant to wear, used in automotive parts.
Each material has unique properties, so the selection depends on the specific requirements of the product.
The Injection Molding Process
Here’s a step-by-step look at how injection molding works:
- Clamping: The mold is held securely in place.
- Injection: Molten plastic is injected into the mold cavity.
- Cooling: The material cools and solidifies.
- Ejection: The finished part is removed from the mold.
- Repeat: The process starts again for the next part.
It’s a straightforward process, but precision at each step is critical to ensure quality.
Applications of Injection Molding
Injection molding is used in countless industries. Here are some examples:
- Automotive: Dashboard panels, bumpers, and interior components.
- Medical: Syringes, surgical instruments, and diagnostic devices.
- Consumer Goods: Toys, kitchen utensils, and storage containers.
- Electronics: Housings for gadgets, connectors, and switches.
The versatility of injection molding makes it invaluable across various sectors.
Cost-Effectiveness of Injection Molding
One reason injection molding is so popular is its cost-effectiveness. While the initial investment in molds can be high, the cost per part decreases significantly with large production runs.
Additionally, the process minimizes waste, as excess material can often be recycled. For businesses looking to reduce production costs, injection molding is an excellent option.
If you’re considering outsourcing your production, partnering with a trusted supplier like this China injection molding company can help you achieve cost savings without compromising on quality.
Challenges in Injection Molding
Like any manufacturing process, injection molding has its challenges:
- Defects: Warping, sink marks, and flash are common issues.
- Material Selection: Choosing the wrong material can lead to poor results.
- Tooling Costs: High upfront costs for molds can be a barrier.
However, these challenges can be managed with proper planning and by working with experienced professionals. Companies like this plastic mold supplier specialize in providing high-quality molds that reduce defects and improve efficiency.
Sustainability in Injection Molding
Sustainability is becoming increasingly important in manufacturing. Injection molding can support eco-friendly practices in several ways:
- Recycled Materials: Using recycled plastics reduces waste.
- Energy Efficiency: Modern machines consume less energy.
- Biodegradable Plastics: These materials break down naturally, reducing environmental impact.
By adopting sustainable practices, manufacturers can meet consumer demand for greener products while reducing costs.
Choosing the Right Injection Molding Partner
Finding the right partner is crucial for successful injection molding. Here’s what to look for:
- Experience: Choose a company with a proven track record.
- Capabilities: Ensure they can handle your specific requirements.
- Quality Assurance: Look for certifications and quality control measures.
- Communication: A reliable partner will keep you informed throughout the process.
For example, this injection molding company in China offers expertise and cost-effective solutions for businesses worldwide.
Future Trends in Injection Molding
The injection molding industry is constantly evolving. Here are some trends to watch:
- Automation: Robots are increasingly used to improve efficiency.
- Smart Manufacturing: IoT and AI are optimizing production processes.
- Sustainable Materials: The use of eco-friendly plastics is on the rise.
- Customization: Demand for personalized products is growing.
Staying ahead of these trends can give manufacturers a competitive edge in the market.
Conclusion
Injection molding is a versatile and cost-effective manufacturing process that plays a critical role in modern industries. By understanding its benefits, challenges, and applications, businesses can make informed decisions to optimize their production.
Whether you’re looking for a reliable supplier or exploring sustainable practices, injection molding offers endless possibilities. And with the right partner, like this trusted plastic mold supplier, you can achieve high-quality results while keeping costs low.
What's Your Reaction?






